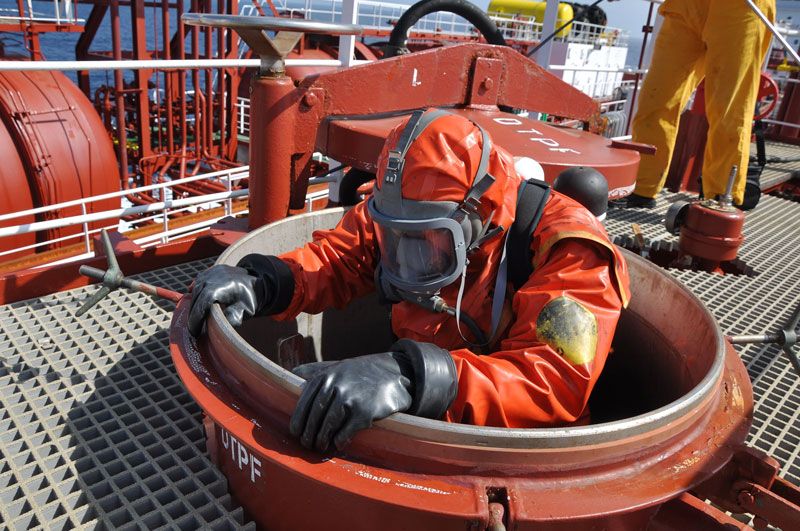
6 Actionable Tank Cleaning Safety Tips for Plant Managers
The presence of toxic and volatile gases can make tank cleaning a highly dangerous activity. As dangerous it is, routine industrial tank cleaning is crucial as an unclean tank can:
- Leak
- Contaminate products
- Corrode due to grime and scale formation
To ensure the safety of workers, facility, environment and brand reputation, make safety checks a priority before each tank cleaning process.
Following are 6 tips you can implement to eliminate the possibility of tank cleaning accidents.
1. Preplanning
Preplanning helps carry out the tank cleaning process smoothly. If you have hired a tank cleaning service in Utah, your staff must collaborate with their staff to see through the success of the operation.
Entry in confined spaces requires a permit from OSHA (the confined space doesn't have to be a tank in particular).
Tank cleaning poses a variety of challenges and hazards, such as:
- Entrapment
- Mechanical
- Electrical
- Chemical
- Oxygen deficiency
- Slip and fall
- Toxic gases
- Toxic fumes
- Combustible dust, etc.
Every accident or hazard needs to be accounted for so that your cleaning service team is prepared to respond.
During the same phase, duties can be assigned to the entrants, attendants, and supervisors.
Communicate warning signals and prohibited conditions to your tank cleaning service company so that everyone on site receives alerts if they suspect any danger.
2. Training and Rescue
Familiarize the tank-cleaning company's staff with the facility’s exit routes.
It's the responsibility of the employer to train their staff and brief the hired tank cleaning company about emergency procedures. You can even teach the basic functioning of the involved machinery so as to increase the tank cleaning company's qualification to deal with the emergency. Spend at least a week training workers and conduct mock drills.
Ensure that everyone in the facility has knowledge and understanding of the training. Urge them to get any questions resolved as soon as possible.
3. Setting Up Tank Entry and Cleaning
Tank entry is set up to minimize the risks for entrants. To make tank conditions favorable, ensure that there is:
- Adequate lighting
- Sufficient ventilation
- Elimination of possibility of slip and fall accidents
- Checking the tank for leakages
- Installing warning signs
- Oxygen supply for the entrants
- Fast availability of a medical professional and first-aid
- Availability of clean water
- A reliable communication system between attendants and the entrant
Further, any recoverable products should be removed from the tank. It includes the removal of sources of ignition, materials of electrical classification and any residue of the material previously stored in the tank.
These steps will greatly reduce the chances of a fire, explosion, electric shock, and exposure to toxic gases and radiation.
4. Tank Isolation
Isolating the tank means creating conditions that restrict the entry or escape of any material or energy into or from the tank. This prevents leakage and environmental pollution. Simultaneously, it also eliminates the possibility of anything entering into the tank and posing a hazard.
OSHA suggests “blanking and blinding” for tank isolation. By installing a skillet or spectacle blind between pipe flanges you close the entry points into the tank. Misaligning or removing a section of pipe achieves the same result.
Hazardous energy also needs to be factored in during the tank isolation process. It poses the danger of electrocution, amputation, death, burns, cuts, laceration, etc. Hazardous energy is stored in the form of:
- Mechanical energy
- Hydraulic energy
- Thermal energy
- Chemical energy
- Stored energy
- Electrical energy
For example, a stuck conveyer belt might go off while a worker is working on unjamming it, which could severely injure the worker.
The tank is isolated from hazardous energy using tagout/lockout which involves disabling machinery and equipment, disabling mechanical linkages, and controlling energy outlets.
OSHA has issued a fact sheet explaining the necessary steps of a tagout/lockout procedure.
5. Degassing the Tank
Residual toxic vapors of previously contained Volatile Organic Compounds (VOCs) pose health risks such as:
- Irritation of eyes, nose, and throat
- Headache, loss of coordination
- Central nervous system damage
If these gases seep into the environment, workers on site without PPE kits are at risk of coming into contact with it. Large quantities of VOCs can contaminate underground water and air.
Tank degassing is accomplished by using a thermal oxidizer or enclosed flair. In the process, the gas is thermally cracked and hazardous vapors are removed before the gas is released into the air.
If you don't have the degassing equipment at your facility, you can take the help of a Utah tank cleaning service. Professional tank cleaners already have the skill to see that the whole procedure is conducted safely and can help you adopt all the best practices so that EPA doesn't charge you with a penalty.
6. Select the Right PPE for your workers
PPE (Personal Protective Equipment) is classified into four different levels: A, B, C, and D.
With the increasing protection, the cost of PPE and the level of ongoing training required to use it increases. So, it's best to analyze the tank cleaning hazards, based on the size and type of tank as well as the material stored in it.
Level A and Level B PPE contain a breathing apparatus, which might not be necessary if a respirator (present in Level C PPE) does the job.
Need Help with Tank Cleaning?
Enviro Care is a Utah-based tank cleaning company. We help clients increase efficiency and sustainability through our tank-cleaning service.
We work on all types of tanks and tankers. Underground, above ground, floating roof, fixed roof - whatever your tank type is, we offer cost-effective and environmentally sustainable solutions. We can kosher wash your tank as well, allowing you to store and transport kosher food in it.
Our team is trained to work in hazardous environments and ensure the safety of workers on the site and the residents nearby. We can also inspect a tank and monitor its rate of corrosion.
When we are done cleaning, we will haul away all the waste and byproducts from your facility and dispose of it responsibly.
We have worked on numerous facilities and collaborated with their teams for a fast and efficient cleaning process. So if you want to get your tanks cleaned quickly so that they can return to operation, call us today!